Step by Step Guide of the process
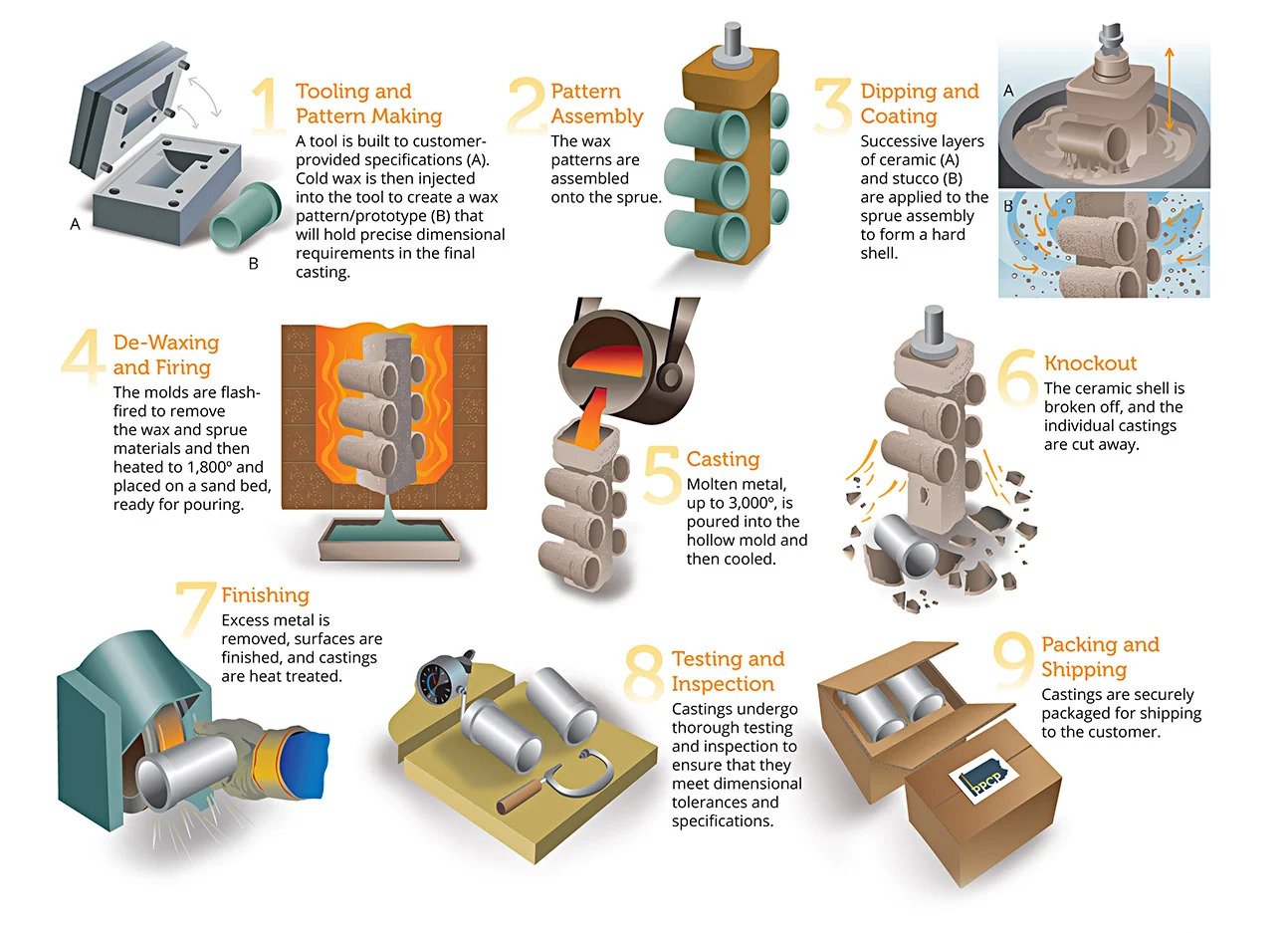
Die Making
The very first and the most important step. The customer can either provide us with the 3-D drawing or even the original product, we provide Reverse Engineering services to ensure quick and accurate die-making.
Wax Injection
The wax design of the desired castings is produced by injection molding. These designs are called patterns.
ASSEMBLY
the patterns are attached to a central wax stick, called a sprue, to form a casting cluster or assembly.
SHELL BUILDING
The shell is built by immersing the assembly in a liquid ceramic slurry and then into a bed of extremely fine sand. Up to eight layers may be applied in this manner.
DEWAX
Once the ceramic is dry, the wax is melted out, creating a negative impression of the assembly within the shell.
Pouring
In the conventional process, the shell is filled with molten metal by gravity pouring. As the metal cools, the parts and gates, sprue, and pouring cup become one solid casting. We have the capability and experience to deal with metals such as Steel and stainless steel alloys according to DIN, EN, ISO, ASTM, BS, and JIS.
Special materials based on Cobalt and Nickel.
KNOCKOUT
When the metal has cooled and solidified, the ceramic shell is broken off by a vibration or knock-out machine.
CUT OFF
The parts are cut away from the central sprue using a high-speed friction saw.
FINISHED CASTINGS
After minor finishing operations, the metal castings become identical to the original wax patterns and are ready for Machining and packed for shipment to the customer as per requirement.
Machining
We also provide all CNC machining options and conventional processing machining.
Surface Treatment
Different surface treatment services are also provided by us such as Galvanizing, Annealing, and Carburizing.
Test Options
In order to ensure customer satisfaction we also provide test certificates by conducting various tests such as analysis by X-ray spectrometer, mechanical values for tensile strength, yield point, impact strength, X-ray, pressure test up to 200 bar.